We’ve seen the global demand for chemical products grow, and with that growth comes new business challenges and demands. Most chemical producers are faced with volatility in the cost of feedstock, a complex regulatory environment, and an aging infrastructure. To make things more difficult, the volume of knowledgeable and skilled workers is shrinking. Not easy scenarios to navigate.
We can guide you through these instances. Whether it be reviewing your process control system, upgrading your legacy systems, or getting the most from the data you generate, we can advise you and help keep you competitive in this dynamic industry. Not sure where to start? Then, check out this eBook and video about The Connected Chemical Plant. They may help you prioritize your current needs.
Improve Your Chemical Plant's Energy Efficiency
Energy is expensive and you want to use as little as possible without negatively impacting your operations. This also plays well if you have an energy management program or broader sustainability effort. Either way, saving energy equates to reduced operating costs and a more efficient plant. Who wouldn’t want that?
Well, did you know there’s an easy first step towards improving energy? Start by using variable frequency drives (VFDs) on your motors, pumps, and compressors to reduce energy use. Answer a few easy questions and our calculator will calculate estimated cost savings. And, if sustainability is important to you, our calculator will estimate the percentage of carbon reduction a VFD can offer, too.
Try our VFD energy savings calculator and see how much you could save.
How to Future-proof Your Operations
Kalypso-delivered Solutions
Kalypso joined the Rockwell Automation family in May 2020 to deliver comprehensive digital transformation services to manufacturers. Kalypso supports many industries - including the chemical industry – with consulting, implementation and managed services, from assessing digital readiness and building a business case, to implementing and integrating technologies, and sustaining the change.
-demo-video/chemical-industry-augmented-reality-demo-video-image.jpg)
Chemical Process Control Solutions
Chemical Process Control for Improved Operations
Open communication platform. Real-time information. Scalable for small and large plants. Are these your big three? Then, PlantPAx, the modern DCS, may be the system you’re looking for.
Our PlantPAx DCS gives you more information about the equipment and the operator performance. This can help with downtime, throughput, and quality issues. More benefits of this solutions are:
- Solutions ranging from single unit to enterprise-wide systems
- Comply with ISA-88 complete with recipe IP protection
- Automate manual operations to reduce variation
- Create repeatable and controlled operations that maximize asset utilization
- Manage recipes and procedures so you can focus on yield, throughput, and quality
- Procedural models which allow you to improve traceability, reporting, and approval control
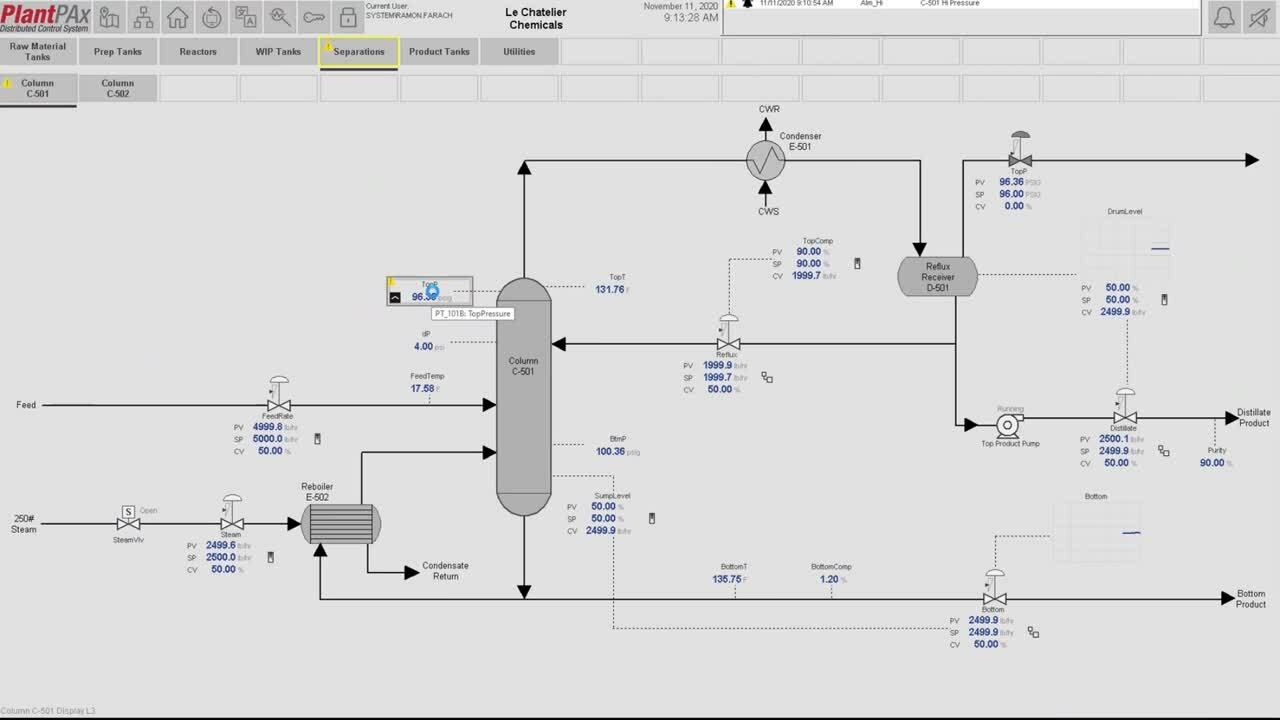
Scalable Model Predictive Control
Pavilion8® modular software platform is the foundation for our industry-specific solutions. This software platform includes modules to control, analyze, monitor, visualize, warehouse, and integrate, and combines them into high-value applications. Scalable, flexible, and easy to integrate with existing business and plant infrastructure, Pavilion8 is better than alternative technologies.
How to Plan and Implement a DCS Migration
Minimize Your Downtime and Maximize Your Success
Most chemical producers feel overwhelmed by the thought of a DCS migration. Well, it doesn’t have to be that bad. Of course, we will help you plan, implement, and test your new system. But, you can benefit from the knowledge we’ve gained by helping thousands of other companies do similar projects. We’ve helped our customers migrate from legacy DCS, PLC, and single-loop controller systems.
We can also help with:
- Installed base assessment
- Information and reporting needs
- Networking and cybersecurity reviews
- BPCS, SIS, and AC&O application audits
- Electrical, instrumentation, and control assessments
- Motor control and drive integration review
- Project justification and cost estimating
- FEED studies
Chemical Safety: Protect Your People and Processes
Are Your Safety Instrumented Systems up to Current Standards?
It’s the nature of this business. Most chemical processes present potential hazards. Some of these hazards can have an adverse effect on people, assets, the environment, or your market perception. A correctly designed, installed, and maintained safety instrumented system (SIS) can reduce that risk.
Whether you are facing an expansion, a new process, or upgrades to existing SIS, ESD, BMS, or TMC, we can help. Get the facts from an experienced functional safety certified engineer. They witness many different scenarios. So, they’re poised to offer direction on both process and machine applications. The technologies that we deploy are scalable from small to large, simplex to triplicated, and capable of up to SIL 3. We provide full lifecycle services to support you in design, build, operation, and maintenance of your chemical process safety solutions.
How Chemical Production Solutions Can Help
Across the world and in all types of chemical plants, we help customers reduce costs, minimize downtime, and improve operations. Whether you seek to modernize your operations, optimize your energy consumption, or enhance your chemical process control, we can help.