Every day, Ecolab helps advance food safety, maintain clean and safe environments, and optimize water and energy usage at nearly 3 million customer sites around the world.
Supporting that mission are Ecolab’s 130 global plants. But until recently, those plants lacked coordination and consistency from one to another. As a result, each plant essentially acted as an individual entity.
Now, Ecolab’s global network of plants is on a five-year roadmap to greater connectivity so they can perform better and more consistently, and ultimately better serve customers.
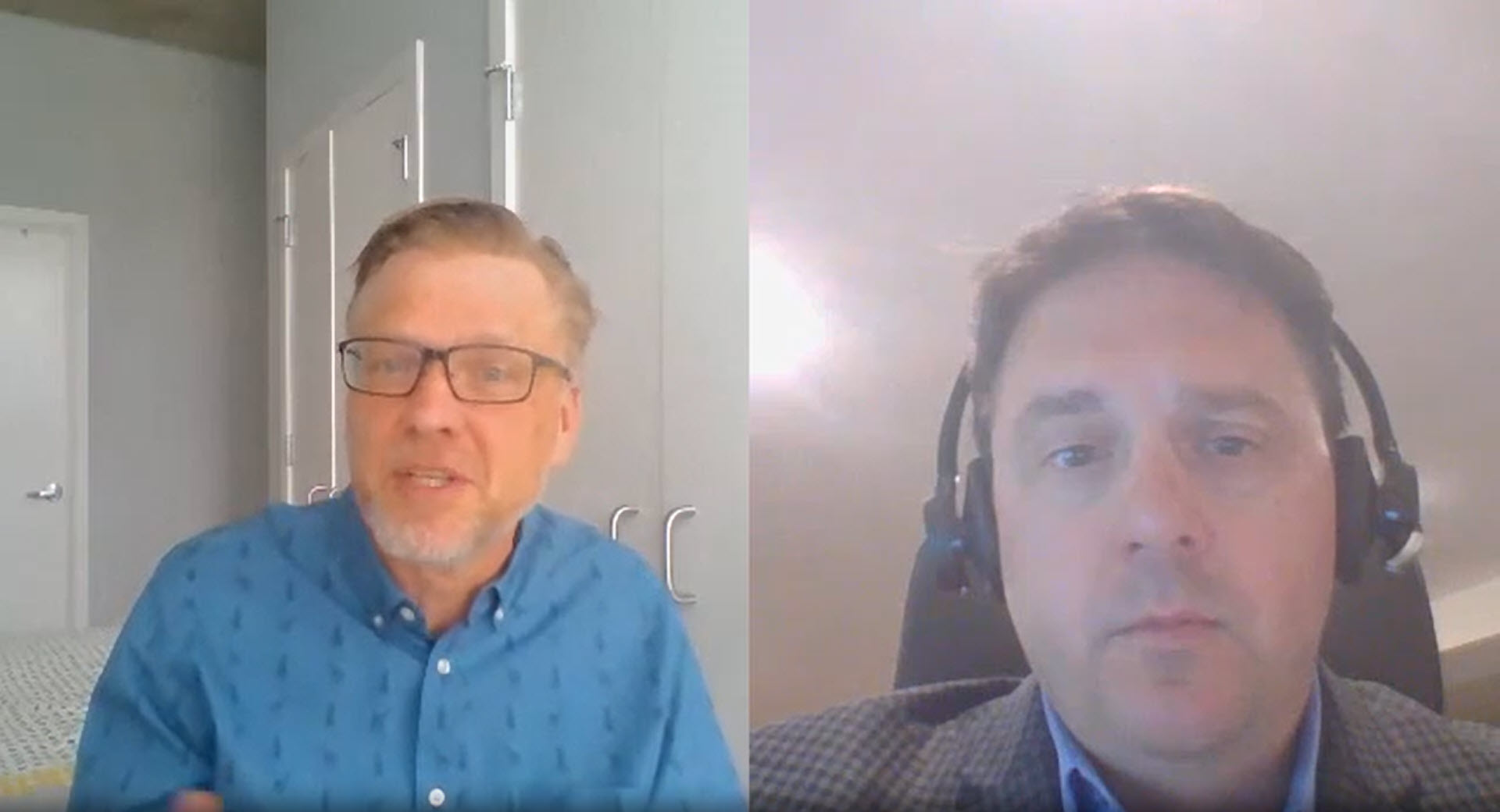
Laying the foundation
Matt Boudjouk, control and automation program lead at Ecolab, was hired to lead the company’s digital transformation.
“My job really is not only to improve the control schemes but also be a conduit of knowledge and share knowledge between plants,” Boudjouk said. “We’re obviously a good-size company, and if we’re not talking to each other we’re not taking advantage of it.”
To connect employees across Ecolab’s plants and give them access to a single data set, Boudjouk formed a team of 20 control engineers representing all of the company’s regions. Together, they created specification standards for how controls and automation should work. This helped break down silos by moving plants away from different technologies and control schemes.
“One of the first specifications that we put together was the cybersecurity hierarchy and network architecture,” Boudjouk said. “We followed a lot of the guidelines that are out there. A lot of it has to do with zoning, adding the proper firewalls, having the proper Ethernet switches. That was very pivotal to have that in place.”
The team also developed an automation strategy. This was the company’s vision for its factories of the future. It included elements like using unified approaches for instrumentation and plant data, so tags from digital applications would make sense whether they were going from plant to plant or up into enterprise systems.
A four-step strategy
From the team’s work arose a four-step strategy for digitally transforming Ecolab plants.
First is the data-gathering step. This involves putting in the right instruments and collecting the right data, all on an Ethernet infrastructure. Documentation is key in this stage to make sure data can be identified and analyzed at later stages.
The next step is the visibility. That’s where plants start monitoring operations and dashboards give operators real-time insights into how their lines are performing.
The third step is business optimization. This involves integrating the plant floor with enterprise systems to provide visibility and communications across plants and the supply chain.
The fourth and final step is digital transformation through the use of capabilities like analytics, digital twins and artificial intelligence on a local and global scale. This can help answer key questions like why some plants perform better than others. Analytics on filling machines, for example, help explain why some machines run better than others, such as because of equipment or training issues.
Results so far
The expectation isn’t to digitally transform all of Ecolab’s 130 plants within the 5-year roadmap but rather to make significant progress in moving them through the four-stage journey.
Already today, some plants are at the optimization stage. And standardization efforts combined with greater global visibility have helped the company save 25-30% on process design. Getting a better handle on inventory and days-on-hand has also been a big opportunity for improvement.
Given the disruptive nature of digital transformation, training has been key. Ecolab has worked with its vendors to establish training programs, including on-site training labs at some plants, to allow employees to interact with and learn new technologies.
“A lot of our automation vendors have local distribution places very close to our plants, so we work closely in conjunction with them to get training for our facilities,” Boudjouk said.
Published December 1, 2020